Schermerhorn Symphony Center
Knockdown Air Handlers with FANWALL TECHNOLOGY® Help Schermerhorn Symphony Center Recover from Flood
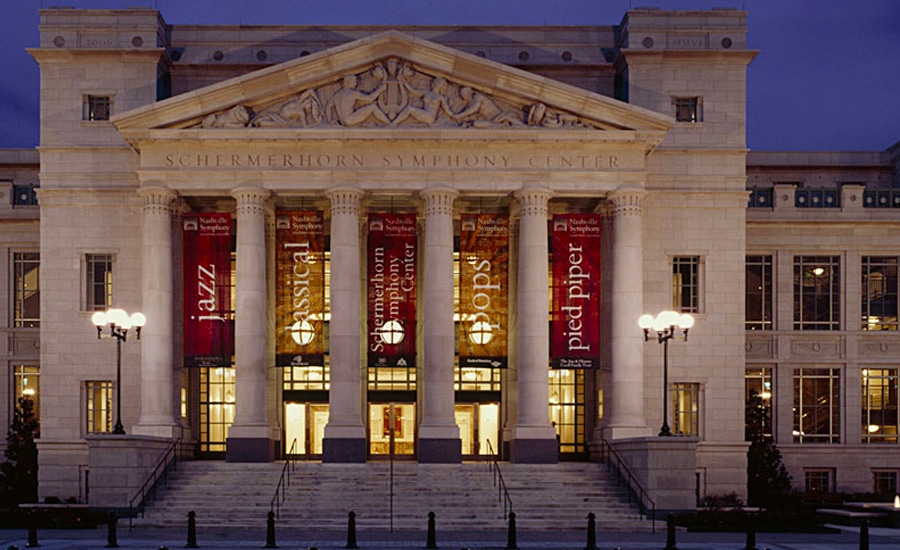

At A Glance
During the first two days of May 2010, a nearly 14-inch downpour fell on “Music City USA” and the Cumberland River burst its banks, causing the worst flood in Nashville’s history. Among the businesses that suffered terrible losses during the flood was Schermerhorn Symphony Center, completed just four years earlier and home of the Nashville Symphony. Floodwaters rose too fast for officials to take preemptive action and musical instruments as well as mechanical systems in the basement were destroyed. To replace a number of damaged air handlers, the mechanical contractor chose our Knockdown Air Handlers with FANWALL TECHNOLOGY and Coplanar Silencers®. Besides providing the necessary airflow for the Symphony Center, the air handler system helped the contractor meet the job’s formidable challenges concerning access, space savings, and acoustical excellence.
“Using FANWALL TECHNOLOGY, the units meet or exceed the acoustic specs of the previous units and perform exceptionally well from when we turned them on.”
Equipment
Design Features Keep Noise Down
“Symphony Hall is an acoustically perfect little building,” said Swartz. “The reason the building works as well as it does is because everything that makes noise is buried in the basement. Our original air handling units were extremely superior pieces of equipment with, among other things, double-lined ductwork to stop noise and vibration. However, those units were placed in the building when it was still a hole in the ground, so in addition to the retrofit issues, we needed something quiet.”
Using Preferred Noise Criteria (PNC), an indoor noise measurement system, the Symphony Center’s designers required a low PNC-30 in the areas surrounding the performance hall and an extremely low PNC-10 in the hall itself. To reach these levels, the original air handling units had four-inch-thick panels with fiberglass insulation between two sheet-metal layers. Similar noise-attenuating panels are installed in the ductwork connected to the air handlers.
“Using FANWALL TECHNOLOGY, the units meet or exceed the acoustic specs of the previous units and perform exceptionally well from when we turned them on,” said Swartz. Small fans operating at relatively high speeds produce less of the troublesome low-frequency noise than lower-speed larger fans. Careful attention to balance of the fan wheel in each modular FANWALL cube significantly reduces vibration. Another key to noise reduction is the patented Coplanar Silencer of each FANWALL cube, which surrounds the fan and motor with acoustically absorbent material to greatly reduce airborne noise at the source.
In most octave bands, the units with FANWALL TECHNOLOGY were more than a 15 dB improvement over the Symphony Center’s old air handlers. As a result of this superior acoustical performance, Tom Barrow Co. was able to eliminate over 25 percent of the sound-attenuation structure installed in the ductwork of the air-handling systems, according to Blystone. In addition, the six air handler systems serving the performance hall required much less sound-attenuating paneling than their much larger “stacked” predecessors.
Benefits of Nortek Air Solutions Knockdown Air Handlers Include:
- Expertise and processes developed over thousands of applications help minimize downtime.
- Components and parts, including the FANWALL cubes, can be navigated through standard 3-foot doors to minimize any cost or disruption from structural demolition and reconstruction.
- The space savings resulting from using a FANWALL system can allow mechanical space to be reconfigured.
- Ancillary components such as sound attenuators and air blenders may also be removed for further space savings and to eliminate static pressure penalties.
- The performance of the new system can be upgraded to better match actual capacity and airflow requirements.
KEY POINTS
- Schermerhorn Symphony Center used Knockdown Air Handlers with FANWALL TECHNOLOGY to replace flood damaged air handlers.
- Knockdown Units are designed and assembled as modular components, enabling the new air handlers to be brought into the basement of the Symphony Center without causing structural damage.
- The space savings of FANWALL TECHNOLOGY allow the new units to sit on structural steel platforms raised six feet off the floor of the mechanical rooms, preventing future flood damage.
- Superior acoustic performance, system reliability, and efficiency will benefit the Schermerhorn Symphony Center for years to come.